7.0. مشکلات ایجاده شده در سیلندرهای هیدرولیک
7.1. مشکل هوا در روغن
مشکل هوا در روغن به خصوص در هیدرولیک های متحرک بسیار رایج است. وجود هوا در روغن سه اثر مهم دارد. اینها؛ اثر برش جریان سریع، اثر دیزل و کاویتاسیون است
7.1.1. برش جریان سریع
هوا به صورت محلول یا حل نشده در روغن وجود دارد. هوای محلول مولکولی در تمام روغن های هیدرولیک وجود دارد. . مولکول های گاز یا با مولکول های روغن مخلوط می شوند یا به مولکول های روغن متصل می شوند بسته به نوع سیال، مقدار هوایی که می تواند در آن حل شود متغیر است. این نوع هوای محلول به تراکم پذیری، ویسکوزیته یا آب بندی روغن تأثیر منفی نمی گذارد.
هوای حل نشده در روغن باعث می شود سیال رفتار بسیار متفاوتی داشته باشد، به خصوص در فشارهای پایین (حدود 60 بار). به عنوان مثال، اگر سرعت سیال افزایش یابد، هوای موجود در آن به شکل حباب منتقل می شود.
اگر سیال تحت فشار دارای هوای حل نشده باشد، این هوا فشرده شده و به محفظه آب بندی راه پیدا می کند. سپس، هنگامی که فشار در اینجا کاهش می یابد، حباب های فشرده آزاد می شوند و با انرژی بسیار زیادی منبسط می شوند. نه تنها قطعه آب بندی، بلکه سطوح فلزی پیستون نیز تحت تأثیر منفی قرار می گیرند و زبری سطح افزایش می یابد.
اگر خراش های روی قطعه آب بندی در نتیجه این انفجارها طولی باشد، این شیارهای مویرگی به عنوان یک نازل عمل می کنند. در حالی که سیال در حال شتاب است، یک جریان سریع در این نازل ها ایجاد می کند و بریدگی هایی را در این نواحی ایجاد می کند. در همین حال، ذرات سیال به سرعت از شکاف عبور می کنند، به پشت قطعه آب بندی می رسند و سطح پشتی المنت آب بند را می سایند. اگر مقدار زیادی هوای حل نشده در سیال وجود داشته باشد، این انبساط می تواند دوطرفه پیستون را به دو قسمت تقسیم کند. این نوع آسیب بیشتر درقطعات آب بندی ساخته شده از پارچه آغشته به لاستیک رخ می دهد. دلیل این امر این است که ساختار آن متخلخل تر از یک قطعه آب بندی لاستیکی همگن و نفوذپذیری هوای آن بیشتر است.
با افزایش فاصله شکاف در مرحله طراحی می توان از این آسیب جلوگیری کرد. زیرا در اینجا این نشتی نیست که قطعه آب بندی را فرسوده می کند، بلکه هوای فشرده ای است که از پشت المنت آب بندی خارج می شود. حباب های هوای فشرده نیز به قطعات آب بندی الاستومری همگن نفوذ کرده و در صورت انبساط قطعه آب بندی را فرسوده می کنند. هنگامی که این آب بندی برداشته می شود، به طور کلی مشاهده می شود که سایش روی سطح لبه آب بندی دینامیکی المنت آب بند است، حجم المنت آب بندی گسترش یافته و مواد آن نرم شده است.
در سیستمهای هیدرولیک، شوکهای فشاری نیز میتواند در ضربات کوتاه رخ دهد و حبابهای هوا در سیستم با انرژی گرمایی بسیار بالایی بارگذاری میشوند. در معادله گاز ایده آل، فشار و دما نسبت مستقیم دارند و با افزایش فشار، دما افزایش می یابد و هنگامی که ذرات هوای بارگذاری شده با گرما منبسط می شوند، سطح قطعه آب بندی را با دما و نیروی کششی بالا ذوب کرده و قطعات را از آن جدا می کنند. مطالعات نشان داده است که دمای این حباب های هوا بسیار بالاتر از 200 درجه سانتیگراد است و حتی می تواند به 1000 درجه سانتیگراد برسد. این دما بسته به اندازه حباب هوا قبل از فشرده سازی، فشار، سرعت و بار تغییر می کند.
7.1.2. جریان دیزل
جدی ترین آسیب در سیلندرهای هیدرولیک ناشی از انفجار اثر گازوئیل هوا در روغن است.هوای به سرعت فشرده شده ناگهان به دمای بالایی می رسد که باعث می شود مخلوط هوا و روغن موجود در محیط با سوختن منفجر شود. این در سیلندرهایی که در برابر بارهای متغیر کار می کنند، بیشتر دیده می شود. در حین این انفجار، فشار در ناحیه انفجار باعث افزایش 5 تا 6 برابری فشار کاری اسمی می شود که باعث آسیب به مواد گاید و سطوح فلزی به ویژه المنت آب بند می شود. آسیب به قطعه آب بندی و قطعات ترموپلاستیک به صورت سوختن و ذوب موضعی دیده می شود.
در خاتمه با توجه به خسارات ناشی از اثر گازوئیل، می توان فهمید که کنترل میزان هوای روغن بسیار مهم است. به همین دلیل باید اقدامات احتیاطی برای جلوگیری از ورود هوا به مخزن روغن، پمپ، سوپاپ ها و سیلندرها انجام شود. هنگامی که یک سیلندر در حال تعویض یا راه اندازی جدید است، باید اطمینان حاصل شود که هوا در آن وجود ندارد. در غیر این صورت، برش جریان سریع و جریان دیزل به قطعه آب بندی آسیب می رساند.
به محض اینکه از نقطه اشباع هوای روغن در فشار معمولی فراتر رود، سیستم در خطر است. حتی در زیر نقطه اشباع، خلاء ایجاد شده در سیستم می تواند هوا را از روغن با متراکم شدن جدا کرده و به قطعه آب بندی آسیب برساند (به کاتیون مراجعه کنید). هنگام برداشتن آب بند آسیب دیده در سیلندر مشکل، باید با طراح پیستون و سازنده دو طرفه بررسی شود. زیرا تعویض المنت آب بندی با قطعه جدید مشکلی را حل نمی کند.
7.1.3. کاویتاسیون
هنگامی که یک سیال تحت فشار از یک گلویی، به عنوان مثال یک شیر عبور می کند، سرعت سیال افزایش می یابد. بر اساس معادله برنولی، (Pst+Pdyn = ثابت) هنگامی که فشار دینامیکی به دلیل سرعت افزایش می یابد، کاهش فشار استاتیک ممکن است تا زمانی که خلاء ایجاد شود ادامه یابد. نتیجه این است که هوای اشباع شده در روغن به صورت قطرات بخار آزاد می شود. این پدیده کاتیون نامیده می شود. هنگامی که این قطرات بخار از گلویی عبور کرده و وارد ناحیه فشار می شوند، منفجر می شوند. اگر این انفجار بر روی یک سطح فلزی یا پکینگ و گردگیر اتفاق بیفتد، نیروهای زیادی که در انفجار ایجاد می شود، سطوح آنها را تخریب می کند. به این حالت فرسایش جریان سریع می گویند.
در سیستم هایی که با روغن هیدرولیک کار می کنند، امکان کاویتاسیون بسیار کم است، زیرا فشار بخار روغن بسیار کم است (1.5-2.5 torr) می تواند برای ساییدن حتی سطوح کافی باشد.
0.3 بار است و انرژی آزاد شده می تواند حتی برای خوردگی سطوح فلزی کافی باشد.
نتیجه
وجود هوای حل نشده در روغن یک خطر بزرگ برای سیستم های هیدرولیک است. چرا در روغن هوا وجود دارد؟ چگونه می توانیم از آن جلوگیری کنیم؟
1. هوا در هنگام راه اندازی، جداسازی و مونتاژ در سیستم تولید می شود. هنگامی که یک پمپ، شیر یا پیستون به تازگی به سیستم متصل شده است، یا زمانی که به دلیل نقص یا تعمیر از هم جدا می شود، هوا باید خارج شود. مثلا؛ پمپ ها باید پس از خارج شدن هوا از شاخه های تخلیه با چرخاندن دستی شفت یا قرقره موتور کار کنند، زیرا باید هوا از پیستون ها تخلیه شود و اتصالات لوله یا شلنگ به درستی انجام شود.
2. اتصالات شل باعث ورود هوا به سیستم می شود. استفاده از بست های بی کیفیت عامل مهمی است. علاوه بر این، در سیستم هایی با بارهای شوک و ارتعاشات (به عنوان مثال، ماشین آلات ساختمانی)، اتصال دهنده ها اغلب شل می شوند. به همین دلیل باید بررسی های مکرر صورت گیرد، در صورت امکان از ترکیب کننده های شیمیایی در اتصالات اینگونه ماشین ها استفاده شود.
3. عوامل طراحی ممکن است باعث ورود هوا به روغن شوند. بسیاری از طراحان ماشین در حجم مخزن هیدرولیک و محل پمپ به دلیل مشکلات فضایی در حداقل ابعاد کار می کنند. حجم مخزن روغن، همه کاربران حداکثر.
هنگام استفاده از روغن، باید سطح روغن مورد نیاز برای مکش بهتر پمپ را فراهم کند.
ضمنا برگشت روغن به مخزن نباید از بالا، سریع و به گونه ای باشد که روغن را تکان دهد و نزدیک مکش پمپ انجام نشود. المان های آب بندی سنگین به خصوص در ساخت پیستون های خاصی که در معرض ضربه و ارتعاش قرار می گیرند مانند تجهیزات ساختمانی باید استفاده شود و در عین حال فضای نشتی قطعه آب بندی بیش از حد باقی بماند. قطعه آب بندی باید با یک حلقه گاید پشتیبانی شود.
7.2. مشکل فشار هیدرودینامیک
یکی از مشکلاتی که اغلب در سیلندرهای هیدرولیک با آن مواجه می شویم فشار هیدرودینامیکی است. کوتاه ترین تعریف فشار هیدرودینامیکی زمانی است که فشار در فضای بین قطعات آب بندی در سیلندرهای هیدرولیک و المان گاید به مقدار بسیار بالاتر از فشار سیستم می رسد و باعث تغییر شکل دائمی قطعه آب بندی می شود. قبل از تشریح شکل گیری فشار هیدرودینامیکی، می خواهیم اصطلاحاتی را تعریف کنیم که از آنها استفاده خواهیم کرد.
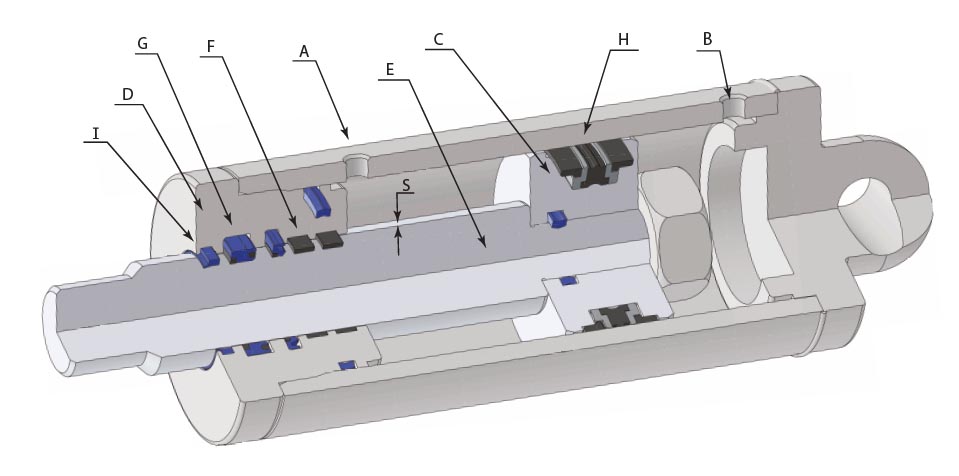
AB: دریچه های ورودی-خروجی سیال هیدرولیک به سیلندر C: سر پیستون
D: گلویی
E: شفت یا میل کروم
F: گاید
G: پکینگ گلویی
H: دو طرفه پیستون
I: گردگیر گلویی
S: فاصله بین شفت و گاید
در تصویر سیلندر هیدرولیک دو طرفه که در شکل 10 مشاهده می کنید، سیال تحت فشاری که از اتصال A وارد می شود، شفت را به سمت راست حرکت می دهد. در همین حال، سیال تحت فشار فضای "S" بین المنت یاتاقان و شفت و فضای جلوی قطعه آب بندی گلو را پر می کند. هنگامی که سیال تحت فشار به خط B سیلندر هیدرولیک وارد می شود و خط A به مخزن تخلیه می شود، میله شروع به حرکت به سمت چپ می کند و با اثر فشار در امتداد حرکت سیلندر حرکت می کند.
در این میان، اگر تلرانس های محکمی در شکاف S اعمال شود، بدیهی است که بیشتر سیال هیدرولیک باقی مانده در اینجا و جلوی آب بند را نمی توان از خط A خارج کرد. در هر مرحله از این فرآیند، مقدار سیال هیدرولیک انباشته شده در اینجا افزایش می یابد، درست مانند یک پمپ کار می کند، فشاری چند برابر بر فشار سیستم ایجاد می کند و باعث تغییر شکل در قطعه آب بندی گلویی و حتی در سیلندر می شود.
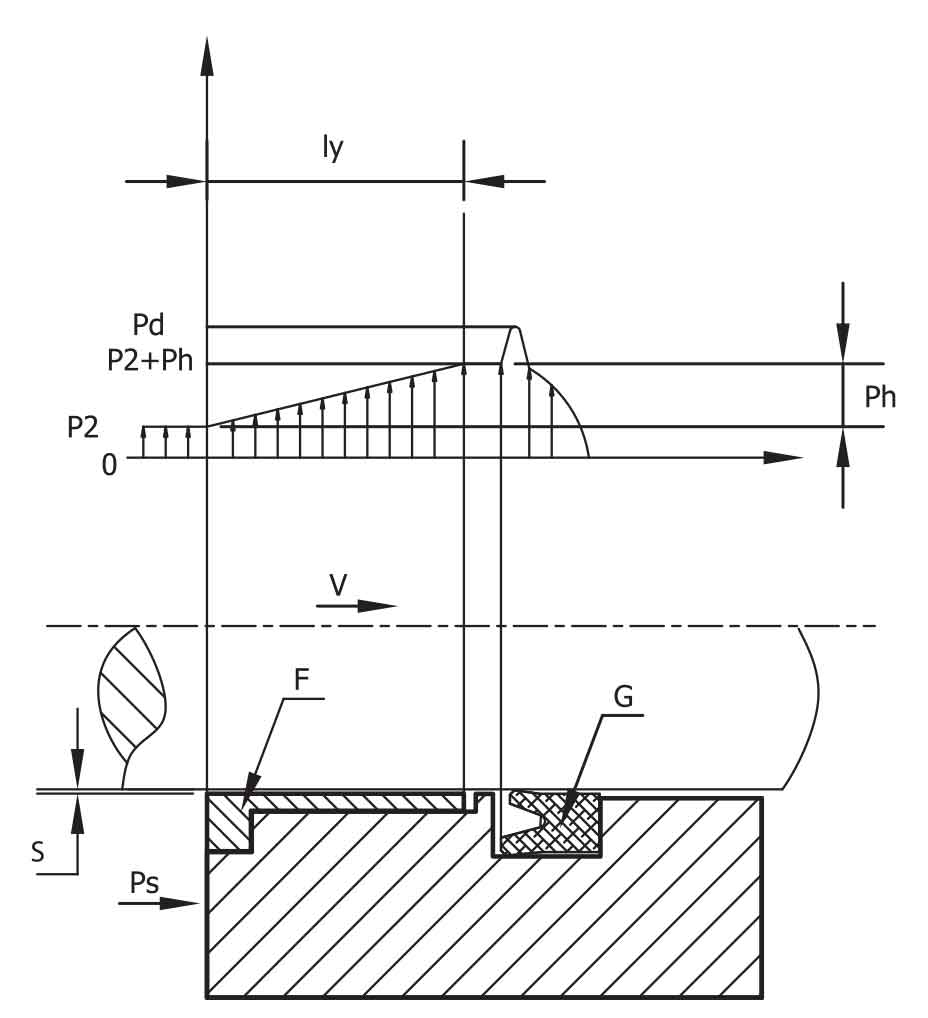
در شکل 11، قسمت گلویی طرح سیلندر هیدرولیک گرفته شده است و جدول داخل افزایش فشار هیدرودینامیکی (ph) را نشان می دهد. مقدار افزایشی با تکرار حرکت را می توان با بیان تجربی زیر محاسبه کرد.
Ph= 6V.LY.1/S2
همانطور که از معادله بالا مشاهده می شود، فشار هیدرودینامیکی مستقیماً تحت تأثیر سرعت لغزش، طول گاید، ویسکوزیته دینامیکی سیال و مقدار فضای بین شفت و گاید قرار دارد.
V=سرعت لغزش (m/sec)
Iy=طول گاید (m)
I= ویسکوزیته دینامیکی (Pa.sec)
S=فاصله بین گاید و شفت (mm)
برخی از پیشنهادات شما راه حل مربوط به پیشنهادات فشار هیدرودینامیکی در زیر آورده شده است. اگرچه کاهش مقادیر عددی (سرعت لغزش، طول یاتاقان، ویسکوزیته دینامیکی) ارائه شده در فرمول فشار هیدرودینامیکی راه حل به نظر می رسد، اما این مقادیر عمدتاً به دلیل طراحی سیستم هیدرولیک نباید تغییر کنند. اگر مقدار فضای بین گاید در مخرج و شفت بزرگ شود، مشاهده می شود که مقدار فشار هیدرودینامیکی به نسبت مستقیم آن کاهش می یابد.در نتیجه بزرگ شدن فضای "S" نمی تواند به عنوان یک قطعه باربر در سیلندر هیدرولیک عمل کند و ممکن است مشکلات بسیار جدی تری با تأثیر نیروهای عمودی بر محور در سیلندر هیدرولیک رخ دهد.
قطعات مورد استفاده به عنوان گاید در سیلندرهای هیدرولیک در زیر آورده شده است.
1. گایدهای رزین فنر (فیبر)
2. گاید ریخته شده
3. گاید برنز
4.گاید های پلی استال (POM) یا پلی آمید(PA)
5. گاید های تفلون اضافه شده (برنز، کربن و غیره)
6. حلقه های فلزی ویژه تفلون اضافه شده
بدیهی است که راه حل ها بسته به نوع قطعه گاید متفاوت است. از تجمع سیالی که ممکن است در سطح جلوی المنت آببندی رخ دهد، میتوان با باز کردن شیارهای مارپیچ روی قطعه چدنی یا برنزی استفاده شده در شکل 12 جلوگیری کرد.
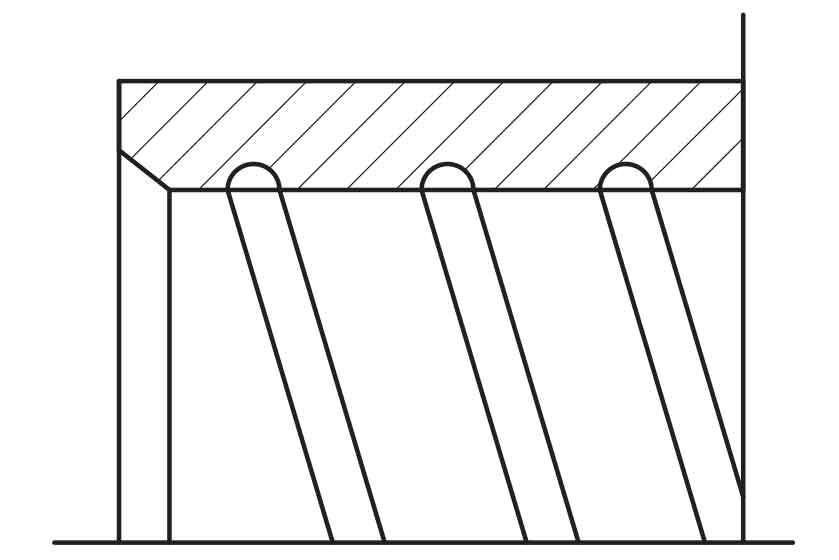
در مواردی که امکان بازکردن این شیارهای مارپیچ وجود ندارد، فشار هیدرودینامیکی را میتوان با باز کردن یک سوراخ تخلیه سریع در شیار قطعه آببندی گلویی که در شکل 13 نشان داده شده است کاهش داد.
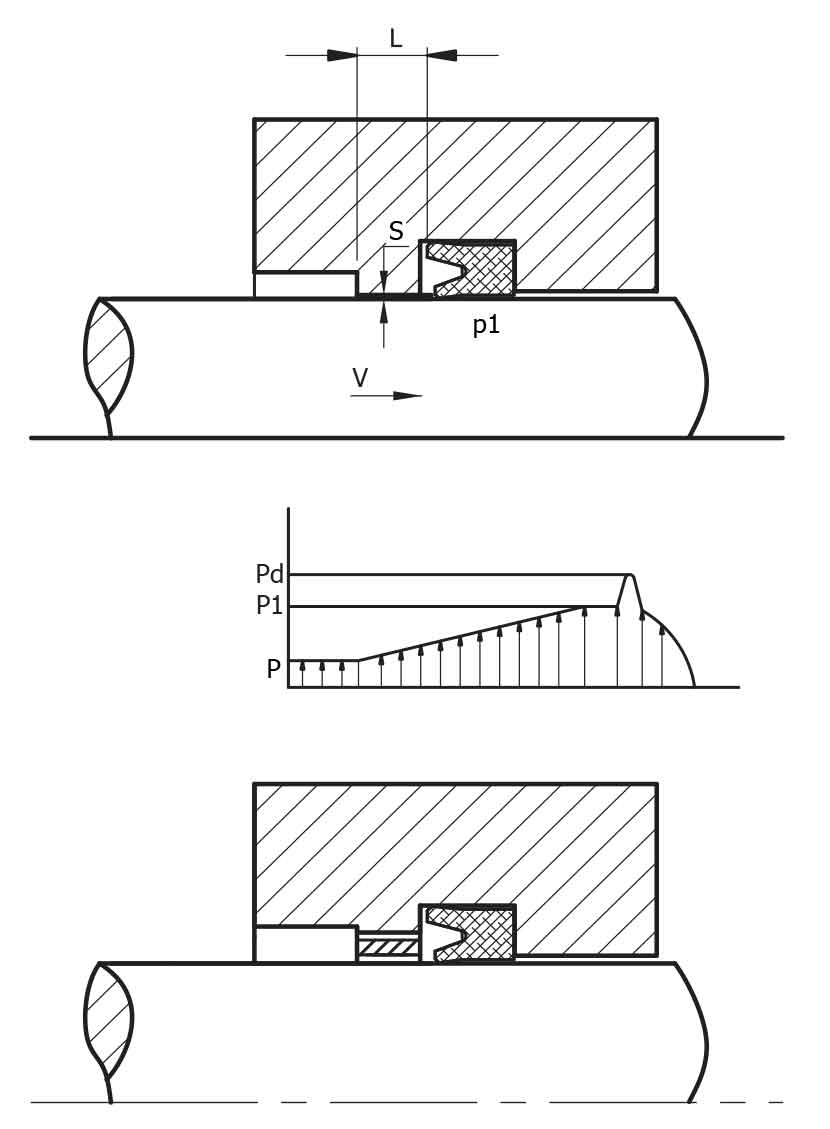
همانطور که در شکل 14 مشاهده می شود، در صورتی که ازگاید نواری استفاده شود، مهم ترین نکته ای که باید در نظر گرفته شود این است که گاید نواری باید از انتها به انتها و به صورت محیطی به هم وصل شود. همانطور که در شکل 13 نشان داده شده است، یک فضای محیطی برابر با فاصله "k" باید بین آنها باقی بماند. سیال هیدرولیک باقیمانده در جلوی آب بند در حین کار باید از طریق این شکاف به سیستم بازگردد.
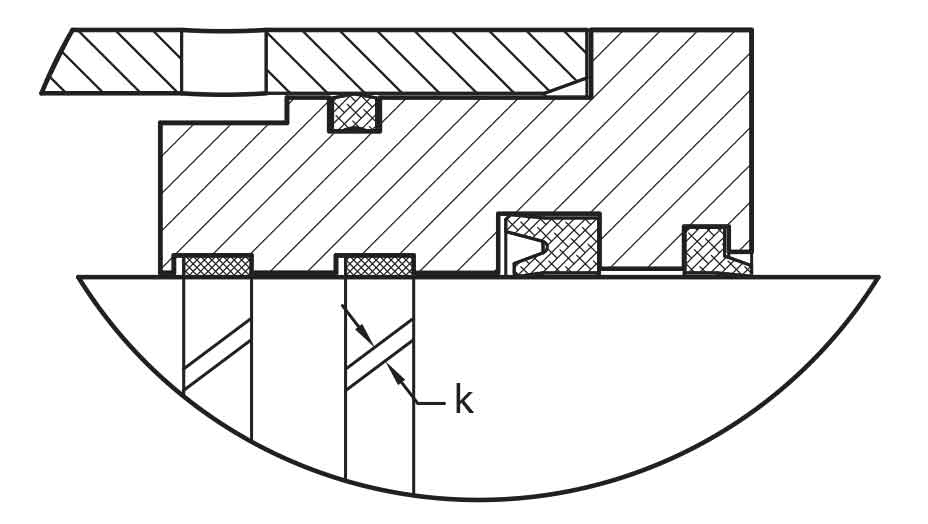
مقادیر فاصله توصیه شده با توجه به مقدار فاصله محیطی (k) که باید در استفاده از گاید نواری داده شود در زیر آورده شده است.
او
|
ک
|
20-40
|
یکی
|
40-70
|
1.5-2
|
70-100
|
2-2.5
|
100-200
|
2.5-3.5
|
200-250
|
3.5-4
|
نتیجه
فشار هیدرودینامیکی ممکن است باعث شود که قطعات سیلندر هیدرولیک همراه با قطعه آب بند هیدرولیک غیر قابل استفاده شوند بنابراین در طراحی و کاربرد سیلندرهای هیدرولیک نباید اجازه ایجاد فشار هیدرودینامیکی داده شود.
8.0. شرایط نگهداری
8.1. محیط، رطوبت و دما
محصولات لاستیکی، پلاستیکی و پلی اورتان باید در جای خشک و خنک نگهداری شوند.
دمای نگهداری باید حدود 15 درجه سانتیگراد باشد و از 25 درجه سانتیگراد تجاوز نکند. رطوبت نسبی باید کمتر از 65٪ باشد. هنگام بسته بندی باید از تماس قطعات آب بند با هوا جلوگیری کرد.
8.2. نور و اشعه ماوراء بنفش
محافظت از محصولات در برابر نور مستقیم خورشید و نور مصنوعی قوی با سطوح بالای UV مهم است.
8.3. اکسیژن و ازون
هیچ وسیله مولد ازون، مانند موتورهای الکتریکی یا دستگاه های فشار قوی نباید در محل ذخیره سازی قرار گیرد.
8.3. تغییر شکل
محصولات لاستیکی نباید تحت کشش، فشار یا خمش قرار گیرند.
صاف قرار دادن محصول برای جلوگیری از له شدن از آن در برابر کشیدگی محافظت می کند و احتمال تغییر شکل را کاهش می دهد.
8.4. تماس با روغن ها و سیالات هیدرولیک
از تماس با مایعات و مواد نیمه جامد به ویژه حلال هایی مانند روغن ها یا گریس ها باید خودداری شود.
8.5. تماس با فلزات
فلزاتی مانند منگنز، آهن و مس یا آلیاژهای مس می تواند به لاستیک آسیب برساند.
بنابراین لازم است از تماس با فلزات یا مواد شیمیایی خطرناک نیز خودداری شود.